So I was busy at home.
It would've been great to get out in the shop, but since the kids were on spring break, most of my time was spent inside the house. When you can't get to the shop, you bring the shop to where you are. Within limits, of course. It meant no lathe work, no mill work, and even my scroll saw was too far from the action to be used. But soldering equipment and software development were fair game.
Two projects got the most time. One was to build a new AutoKAP controller, and the other was to retrofit my Brooxes BBKK KAP rig with a 2.4GHz radio.
The Radio
As often happens on the KAP forums, someone who's just getting started asked some good questions about how to get going, and what to buy. The discussion turned towards radios. I tossed in my two cents, but luckily some other folks did, too. One of them posted a link to a four-channel 2.4GHz radio being sold out of China. Shortly after that, someone posted a link to a six-channel 2.4GHz radio with some ability to program it.
The shipping on the four-channel radio was a little prohibitive, but that's to be expected, living on an island out in the Pacific. The shipping on the six-channel radio was significantly lower, and basically made the extra two channels and programmability a free upgrade. I went for the six-channel radio.
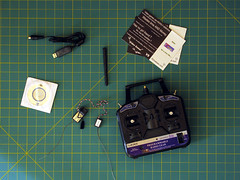
The contents of the package made me smile. There was a very solid 2.4GHz transmitter, a microscopic little receiver, a mini-CD with the drivers and configuration software, a cable, and... no manual. Though there were two $5 coupons with some of the funniest advertising I've ever seen for RC hobbies. It made for some great reading.
My eventual plan with this radio is to gut the transmitter and move the contents to a new enclosure I can clip to my belt or to my backpack strap. Joysticks really aren't the ideal input for doing KAP, with knobs, sliders, and buttons being better choices. Luckily most RC gear uses standard potentiometers on their joysticks, so swapping out a dual-axis stick for two discrete knobs is simply a matter of finding two potentiometers that match the electrical characteristics of the ones in the joystick.
But for now I'm happy to use it as it was made.
The driver and software installed without a hitch, though some of the windows that popped up were in Chinese, and the ones that had been translated to English had some quirks in the translation. On the whole, though, it was fairly straightforward to decipher.
Configuring the axes took a little head-scratching and forum searching. This wasn't made any easier by the fact that every time I powered up the transmitter, my laptop lost its wireless network connection. But eventually everything was sorted out.
The two joysticks map to channels 1-4 on the receiver in one of four "modes" that place the various channels on different joystick axes. I stuck with "mode 1", the default. With KAP gear I don't really care which channel I plug a servo into, so it's a non-issue.
The radio also comes with two switches and two potentiometers with knobs. I wanted to use one to drive the KAP rig's tilt. With the addition of a sticker on the transmitter indicating degrees of down-tilt for each position of the knob, I'd know exactly where the rig was pointed. And this is where the head-scratching really began.
The knobs and switches don't map to any channels. They're generic analog and digital inputs. You can mix them with other channels, use them to select whether a channel is single or dual rate, or to do various other functions. In the end I selected one of the knobs, used it as the input to a mixer function that was set to be on all the time, and tied the output to channel 5. Voila, now that knob goes to channel 5.
The switches were set up to enable or disable a mixing function that tied the other knob to channel 6. With the knob maxed out, flipping either switch sends that channel to its end of travel. Voila, switch-enabled shutter.
Endpoint adjustment has got to be my favorite feature of this radio. Careeful tweaking of endpoints let me set a very precise range for tilt, with one end of the knob's travel taking it exactly horizontal, and the other end taking it exactly vertical. Adjusting the throw of the shutter servo was done in a similar fashion. And when I do eventually convert my rig to the GentLED-CHDK2 for shutter triggering, the same setup will work just fine.
In addition to moving away from an AM radio, this conversion shaved well over a pound off my backpack's weight at a cost that's a fraction of most 2.4GHz radio systems. I'm pleased as can be with it. I just can't wait until the weather clears and I'm able to test this system in the field.
Next time, I'll talk about the AutoKAP controller. That is a completely different story.
-- Tom